
Injection stretch blow moulding
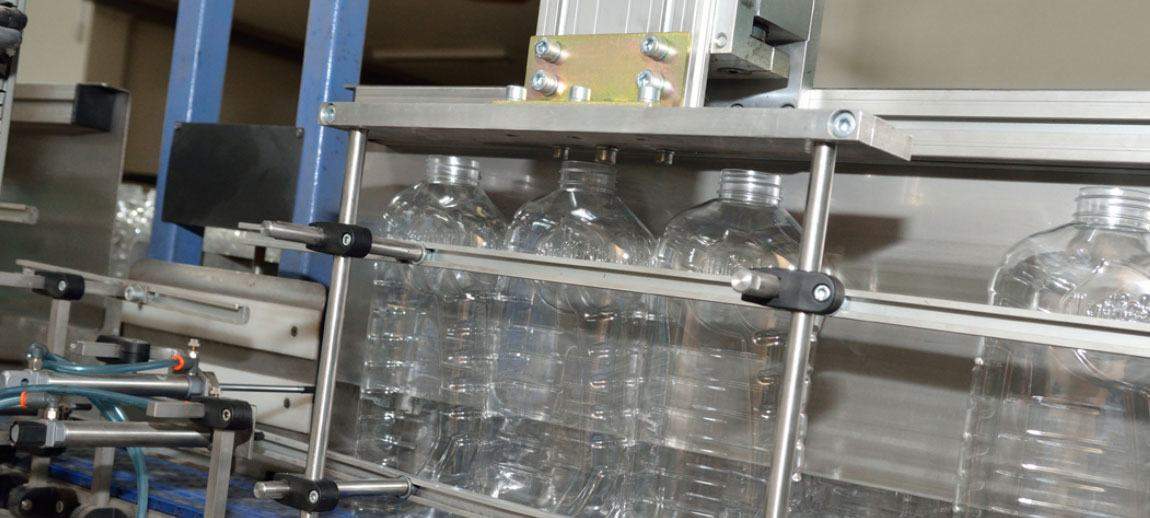
Injection stretch blow moulding – a quick guide
Our injection stretch blow moulding (ISBM) technology is well suited to customers seeking lightweight, thin-walled custom moulded bottles and containers. ISBM is primarily used to manufacture products where the uniform shape or wall thickness is particularly important.
It combines the benefits of two proven technologies – injection moulding and blow moulding:
The injection moulding stage (or preform) precisely defines the neck finish and the weight of the final bottle or jar, significantly enhancing the rigidity of the neck and associated cap performance. This is complemented by the wide range of pack shapes that are achievable via the blow moulding stage.
The process has two variants: single-stage and two-stage. In both variants, the plastic is first injection moulded into a preform, defining the neck finish of the final bottle. These preforms are heated over their glass transition temperature, then blown using high-pressure air into bottles using special blow moulds. At the same time, the preform is stretched with a core rod to increase its rigidity.
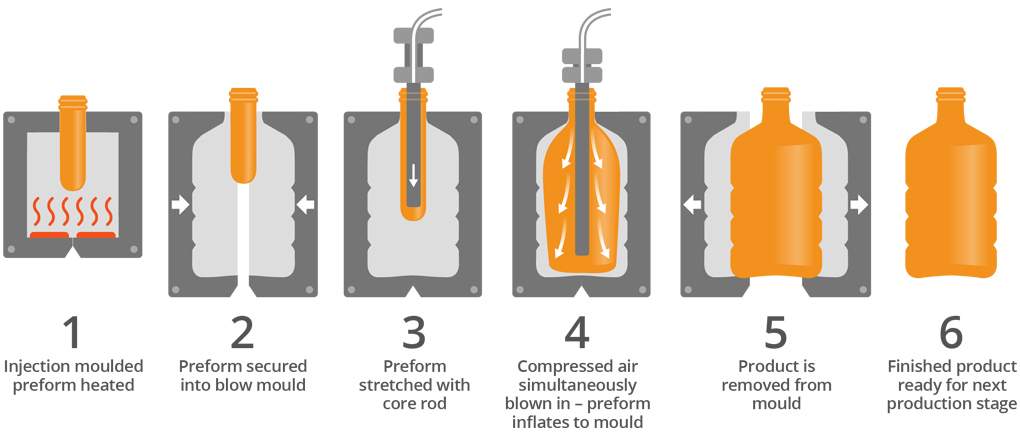
-
Key advantages
- High-speed efficient process
- Dimensionally accurate neck finishes allow for precise product application
- Excellent strength to weight ratio for even the largest of containers
- One preform can produce multiple bottle shapes
- Excellent O2 and CO2 barrier properties for PET bottles
- Reduced weight containers
- Ensures high breakage resistance
- Lightweight crystal clear containers which put the product contents firmly on display, and are lighter and cheaper than their glass counterparts
- Comparatively low mould cost.
-
Examples
- Transparent and coloured sauce and dressing bottles
- 100% rPET shampoo bottles
- Angle-necked toilet cleaners
- Large liquid detergent bottles with handles
- Travel size personal care products
- Housing for room fragrances
- Multi-component assembly for air fresheners
- Irregularly shaped hooks for toilet fresheners.
-
Typical materials
Homo and Copolymer PP and PET (100% post-consumer recycled material (PCR) food-grade resin is available in PET).
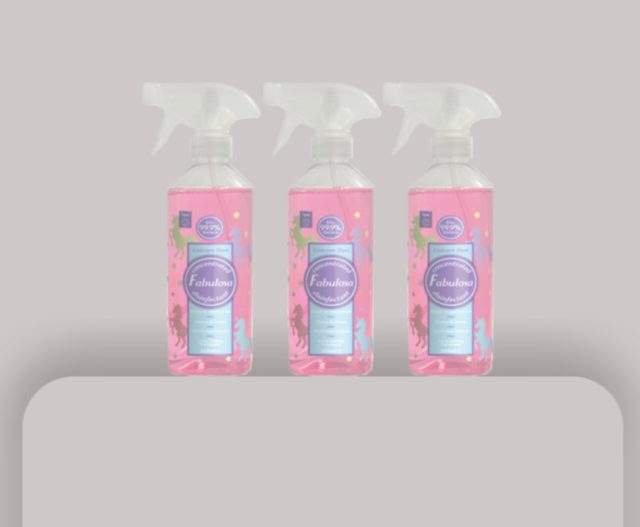
Case Study – Fabulosa
Fabulosa’s highly innovative approach to fragrance and product development has meant that, in less than two years, the family founded and managed brand has taken the market by storm, selling over 50 million products and launching well over 100 beautiful fragrances.
We’d love to tell you more!
Get in touch for advice on the best moulding process for your product.
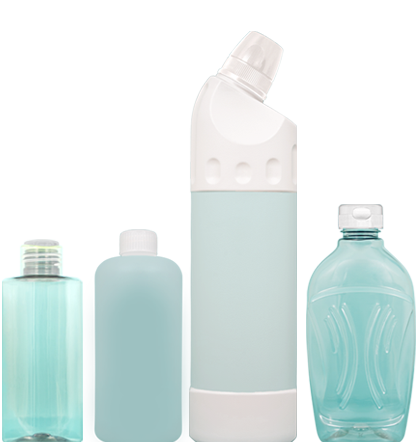