
Blow moulding
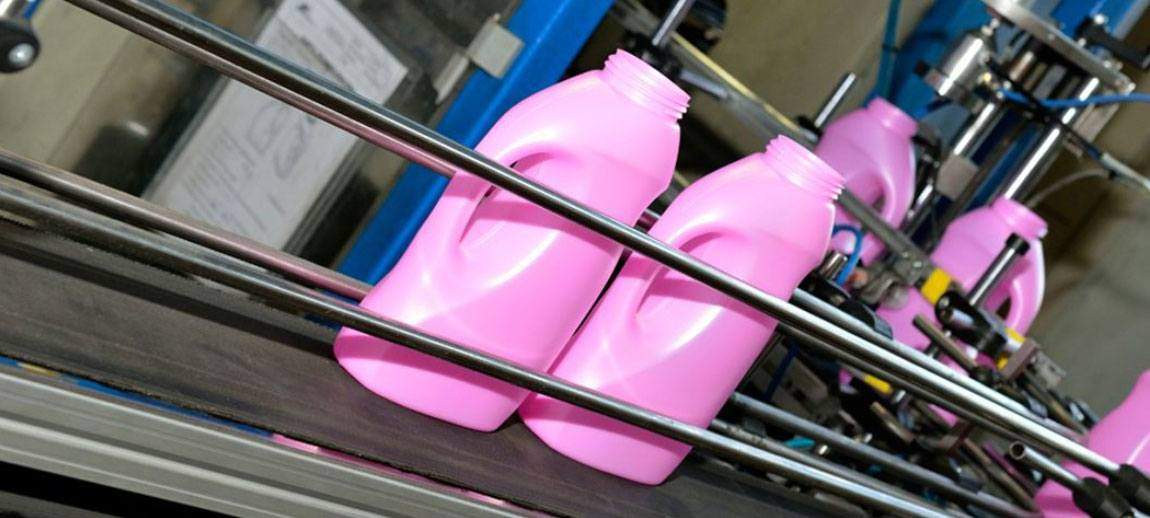
Blow moulding – a quick guide
Blow moulding begins with plastic being melted and extruded into a long, continuous tube. The parison (hollow, continuous tube) is then captured by closing it in a water-cooled mould. Air is then blown into the parison, inflating it so that the plastic can take on the shape of the mould. While similar to injection stretch blow moulding, it’s a die shape and not a mould that determines the shape of the final product.
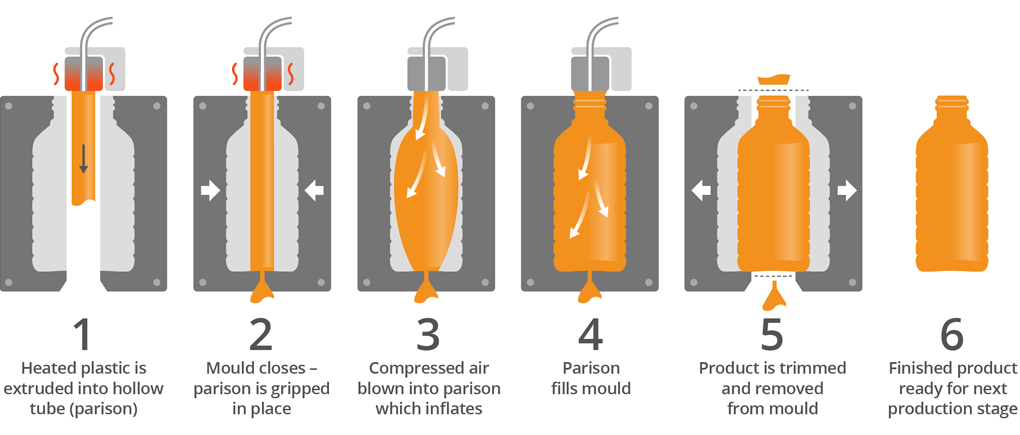
-
Key advantages
- Low investment cost due to the simplicity of the tooling and machinery
- All shapes, sizes and neck types are available using a variety of materials
- Wide range of container shapes
- Dual-layered bottles offer an additional barrier, soft touch, and engaging visuals.
-
Examples
- Personal care ranges such as shampoo and conditioner bottles
- Integral handles
- Trigger sprays
- Jerry cans for the automotive industry
-
Typical materials
PP, HDPE and LDPE.
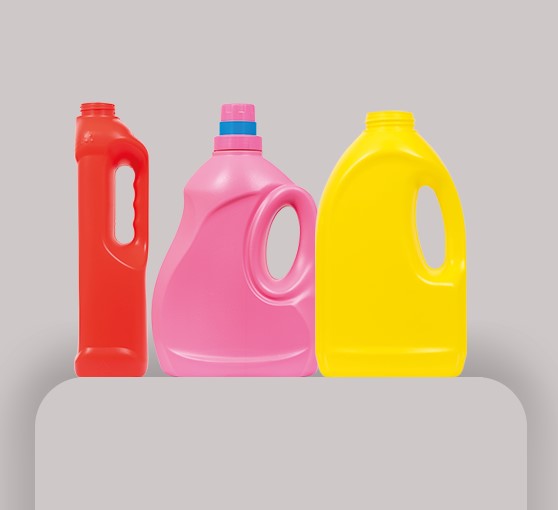
Case Study – Laundry bottles
We’re proud to be the trusted partner for leading FMCG companies across Europe, offering a range of laundry bottles from 1 litre to 3 litres in size, and incorporating many different dosing features.
We’d love to tell you more!
Get in touch for advice on the best moulding process for your product.
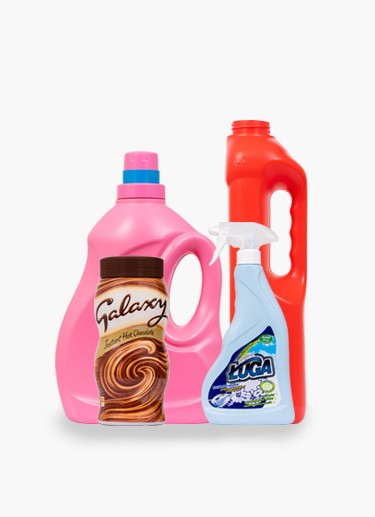
Custom packaging
Need something custom made? The majority of our packaging solutions are custom made. No matter how specialised the requirement, we are known for getting things done.